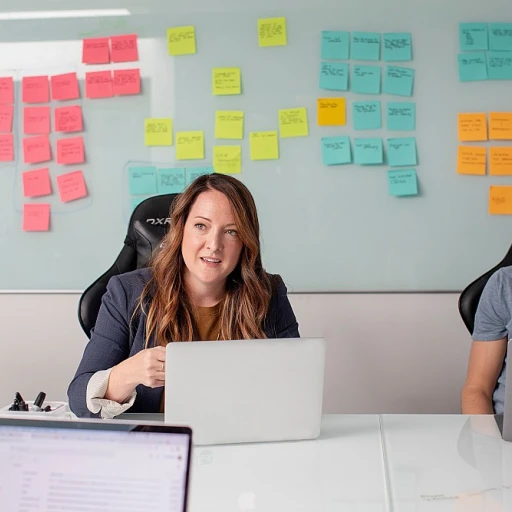
Understanding SIOP Planning
The Foundation of SIOP Planning
Understanding SIOP (Sales, Inventory, and Operations Planning) is pivotal for effective management, as it acts as the heart of strategic and operational decision-making. The process integrates sales and operations planning, ensuring alignment between demand and supply chain activities. This alignment is key for optimizing inventory levels and enhancing production planning. The SIOP process begins with gathering and analyzing key data from various business functions, including sales, marketing, and production. This data forms the basis of strategic planning, allowing businesses to predict demand supply trends effectively. Moreover, the alignment of cross-functional teams is fostered, contributing to efficient customer service and timely fulfillment of demand. By understanding these fundamental aspects of SIOP planning, businesses can better prepare for market fluctuations and adapt their operations accordingly. This understanding also aids in maintaining optimal service levels, ensuring that the inventory meets customer requirements without overstraining production resources. For a deeper dive into the importance of adapting supply chains, explore the insights on understanding and measuring supply chain downside adaptability. This comprehension can significantly enhance your SIOP planning process, enabling more precise sales inventory and operations planning.Key Components of SIOP Planning
Core Elements for Effective SIOP
Understanding the key components of Sales, Inventory, and Operations Planning (SIOP) is essential for achieving optimal efficiency in business processes. This planning model aims to align various facets within an organization, such as sales, inventory, and production, to meet customer demand while optimizing resources.- Demand Forecasting: One of the pivotal elements in a SIOP process is demand forecasting. This involves predicting customer demand over a specified time frame. By leveraging historical sales data and market trends, businesses can anticipate the required inventory levels, ensuring that supply aligns with demand.
- Inventory Management: Managing inventory is crucial in maintaining balance and preventing excess or shortages. The strategic management of inventory helps in maintaining service levels and meeting customer requirements promptly. Tools like inventory operations and inventory levels monitoring play a significant role here.
- Production Planning: Efficient production planning ensures that manufacturing processes support the demand forecast. It's about setting up production schedules that meet the strategic goals of the organization while optimizing resource utilization. By aligning production plans with the sales plans, companies can mitigate bottlenecks and enhance productivity.
- Cross-functional Collaboration: SIOP thrives on the synergy between various departments like sales, marketing, and operations. This collaboration helps in making informed decisions that are supported by accurate data, resulting in cohesive business operations. Adopting a cross-functional approach enables seamless communication and fosters a shared understanding of business goals.
- Decision Making and Data Analysis: Informed decision making is supported by the analysis of comprehensive data sets. Utilizing sophisticated tools for data analysis aids in gauging market trends and adjusting operations planning accordingly. A data-driven approach enhances the company's ability to respond to market dynamics efficiently.
Benefits of Implementing SIOP Planning
Unlocking the Potential through SIOP Planning
The implementation of Sales, Inventory, and Operations Planning (SIOP) offers significant advantages for businesses striving to optimize their supply and demand processes. When effectively deployed, SIOP acts as a strategic framework that helps businesses navigate the complexities of inventory levels, customer demand, and production planning. The benefits of SIOP planning are manifold:- Enhanced Visibility & Alignment: SIOP provides a comprehensive view of the supply chain and aligns sales, marketing, and operations teams. This ensures that everyone is working towards shared objectives, which fosters better decision-making and coordination.
- Improved Inventory Management: The SIOP process helps maintain optimal inventory levels by balancing supply and demand. This not only reduces excessive stock holding but also prevents stockouts, enhancing customer service levels.
- Increased Efficiency: By syncing operations planning with sales forecasts and customer needs, companies can streamline their operations. This alignment reduces waste in the supply chain and optimizes resource utilization, leading to cost-saving efficiencies.
- Data-Driven Decisions: SIOP relies heavily on the integration of time-sensitive data and analytics, empowering businesses to make informed decisions. By leveraging rich data sources, managers can anticipate market trends and adjust their plans proactively.
- Enhanced Customer Satisfaction: By ensuring that customer demand is met more consistently, businesses can improve service levels. SIOP facilitates this by aligning production with the expectations of key customers, ultimately boosting satisfaction and loyalty.
Challenges in SIOP Planning
Overcoming Hurdles in SIOP Planning
As efficient as SIOP planning promises to make operations, it comes with its fair share of challenges. Recognizing these roadblocks in the initial stages can greatly enhance the probability of a seamless implementation process and effective outcome. Here's how organizations can navigate through common difficulties:
- Data Accuracy and Consistency: The integrity of data is vital for successful SIOP planning. Inaccuracies in data regarding inventory levels, sales forecasting, or demand supply can lead to misguided decisions and strategies. Implementing robust checks and ensuring data consistency across the chain management is critical.
- Cross-Functional Conflicts: While SIOP planning inherently encourages collaboration, varying objectives between departments like sales marketing and inventory operations can create tension. Ensuring clear communication and aligning objectives can mitigate this challenge. Regular cross-functional meetings play a crucial part here.
- Supply Chain Complexity: Supply chains are intricate networks that require adept handling. Mismanagement of supply demand and chain management can lead to disruptions. Developing a comprehensive supply chain strategy that incorporates flexibility and adaptability helps in overcoming this challenge.
- Time Constraints: The SIOP process is time-consuming due to the intricate nature of operations planning and production planning. Streamlining these plans and focusing on key priorities can reduce time burdens, enhancing overall efficiency.
- Technological Integration: The rapid pace of technological advancements can overwhelm existing SIOP processes. Companies need to stay abreast of new tools and technologies that can optimize their planning process without disrupting existing systems.
Addressing these challenges not only facilitates smoother operations but also strengthens the organization's capability to respond to market demands. Proper strategic planning and continuous improvement in decision making are essential in minimizing these obstacles. By embracing these strategies, businesses can optimize their operations and achieve optimal customer service levels.
Best Practices for Successful SIOP Planning
Proven Tactics for Navigating SIOP Planning
Ensuring the success of SIOP planning involves methodical execution and strategic foresight. To master the SIOP process, businesses may focus on several best practices that harmonize sales and operations, streamline inventory, and enhance customer service.- Embrace Cross-Functional Collaboration: A key factor in successful SIOP planning is effective collaboration among cross-functional teams. Encouraging open communication between sales, operations, and supply chain management can lead to more cohesive decision-making. This integration is crucial for aligning the entire organization towards shared goals.
- Integrate Data and Technology: Advanced data analytics play a pivotal role in the SIOP process. Leveraging data-driven insights enables businesses to accurately forecast demand and optimize inventory levels. Furthermore, integrating technology in the planning process helps in monitoring and adjusting plans in real time, adding agility to the overall strategy.
- Focus on Strategic Inventory Management: Maintaining optimal inventory levels is essential to balancing production and operations planning. Employ inventory strategies that prevent overstocking or stockouts, thus supporting steady production planning and ensuring that customer demand is met promptly.
- Regularly Review and Adjust Plans: Continuous review of the sales, inventory, and operational plans ensures they stay relevant with market dynamics. Incorporating feedback loops into the process allows for timely adjustments in supply chain operations. This adaptability keeps the business competitive and responsive to changes in demand.
- Prioritize Customer Service Excellence: Ensuring high service levels is integral to maintaining customer satisfaction. Planning SIOP with a customer-centric approach secures a competitive edge. Aligning the operations with sales and marketing teams helps in addressing customer needs and preferences effectively.
Case Studies: SIOP Planning in Action
Real-World Applications of SIOP Planning
In the dynamic landscape of business management, the SIOP process has proven to be a pivotal tool for aligning sales, inventory, and operations. By examining real-world applications, we can better understand how this strategic approach enhances decision-making and optimizes supply chain management.
Manufacturing Sector: Streamlining Production and Inventory
In the manufacturing industry, effective SIOP planning is crucial for balancing production planning with demand supply. A leading electronics manufacturer implemented a robust SIOP process to address fluctuating customer demand. By integrating cross-functional teams, they improved their sales operations and inventory levels, resulting in a 20% reduction in excess inventory and a 15% increase in customer service levels. This case highlights the importance of data-driven decision-making in maintaining optimal inventory operations.
Retail Industry: Enhancing Customer Satisfaction
A major retail chain faced challenges in aligning their sales marketing strategies with their supply chain operations. By adopting SIOP planning, they were able to synchronize their sales plans with inventory management, ensuring that the right products were available at the right time. This strategic alignment not only improved their supply demand balance but also enhanced customer satisfaction by reducing stockouts and improving service levels.
Automotive Industry: Improving Supply Chain Efficiency
The automotive sector, known for its complex supply chain, has also benefited from SIOP planning. An automotive parts supplier implemented a comprehensive SIOP plan to better manage their production and supply chain processes. By focusing on key components of SIOP planning, they achieved a 25% reduction in lead times and a 30% improvement in supply chain efficiency. This case underscores the value of a well-coordinated planning process in achieving operational excellence.
These case studies demonstrate the transformative impact of SIOP planning across various industries. By fostering a culture of collaboration and strategic alignment, businesses can effectively manage demand supply dynamics, optimize inventory operations, and enhance overall business performance.