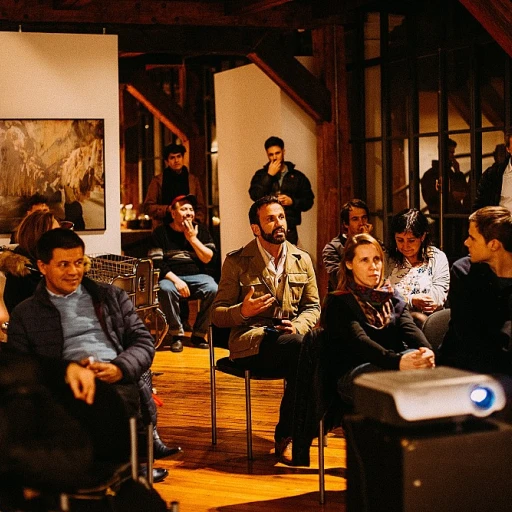
Understanding Service Inventory Management
Grasping the Concept of Service Inventory Management
In today's rapidly evolving business landscape, understanding service inventory management becomes crucial for maintaining efficiency and ensuring customer satisfaction. At its core, service inventory management is all about tracking, maintaining, and optimizing inventory levels—not just of physical products but also of services offered. This concept applies to businesses regardless of where their inventory is stored, be it across multiple locations or in one centralized location. The process involves managing service inventories in real time, which is essential for reducing stock levels and meeting customer demands promptly. Service inventory encompasses more than just tangible products but also includes the 'availability' of services that businesses offer their customers. This could be as simple as ensuring a technician is available for a field service appointment or having the right stock levels of parts for quick repairs. A well-designed management system integrates various components, such as inventory control and supply chain processes, to ensure optimal inventory level management across all inventory locations. By understanding this, businesses can streamline operations and leverage service inventories for competitive advantage. Additionally, one of the keys to successful management is leveraging the right management software. Tools that provide real-time updates on inventory transactions enhance the ability to order and restock items efficiently, ensuring that business operations run smoothly without interruptions. Understanding the Essential Stages of Office Refurbishment also plays a crucial role in understanding how physical spaces can impact inventory systems and enhance service delivery within an organization. As you delve deeper into service inventory management, you'll discover how this process forms the backbone of many logistics and customer satisfaction strategies, reflecting its importance across various business fields.Key Challenges in Service Inventory Management
Challenges in the Dynamic Landscape
Service inventory management is a multifaceted process, and businesses often encounter several challenges when managing their inventory levels. Unlike traditional product inventory, service inventories don't have tangible stock that can be counted or stored in physical locations. Instead, it is about tracking service items, availability, and ensuring customer satisfaction while minimizing delay in order fulfillment.
One significant challenge lies in maintaining optimal inventory levels to meet unpredictable demand. The dynamic nature of service demand requires businesses to adopt systems that can track inventory in real time. This ensures that customer orders are fulfilled promptly, without overstocking or understocking, thereby maintaining a seamless supply chain.
Managing service inventory also complicates inventory transactions and locating service resources. Given the fluidity of service locations, businesses need a robust inventory management system that provides visibility into any available service resources across different locations. Adjusting stock levels according to these varying inventory locations presents another layer of complexity.
Additionally, integrating field service and product inventory within the same management software is a common hurdle. Businesses must manage inventory in a way that scopes both tangible products and intangible service elements while aligning with order processing, supply chain workflows, and customer demand. Therefore, advanced inventory control technologies, such as the weeks of supply formula, are often integral to the process.
Cycle counting, another component of inventory management, ensures that discrepancies are minimized between recorded and actual stock levels. This involves regular checks and reconciliations in inventory control, preventing the risk of service interruption and enhancing customer experience.
Each challenge in service inventory management necessitates a strategic approach tailored to business needs, a topic further explored in the applied strategies section.
Strategies for Effective Service Inventory Management
Proactive Approaches for Boosting Efficiency
Effective service inventory management is vital for businesses that aim to maintain optimal stock levels while meeting customer demands and preventing overstock. Several strategies can streamline the inventory process and ensure efficiency across various locations and services.- Optimal Inventory Levels: Businesses should regularly evaluate inventory levels to maintain the right balance between supply and demand. By monitoring usage patterns and seasonal variations, businesses can adjust their stock levels accordingly, averting potential shortages or surpluses.
- Data-Driven Decisions: Utilizing management software that offers real-time data analytics can significantly enhance decision-making. This not only includes tracking inventory at different locations but also understanding trends in product demands, helping in forecasting and planning.
- Cycle Counting: Implementing cycle counting as an alternative to annual physical counts aids in maintaining accurate inventory records. By regularly checking distinct segments of their inventory, businesses can reduce discrepancies and maintain flexibility in their supply chain.
- Engaging Field Service Teams: As they are often the first point of contact, field service teams should be included in the inventory control process. Training on identifying and reporting stock levels can keep service inventories up to date, thus improving overall customer satisfaction.
- Simplifying the Ordering Process: Streamlining the order process with automated systems or management software can minimize human error, cut down on lead times, and ensure a swift response to inventory transactions.
Technological Tools and Innovations
Innovative Tools and Techniques for Inventory Mastery
In today's fast-paced business environment, harnessing technological advancements is crucial for efficient service inventory management. Savvy businesses are turning to cutting-edge inventory management software to streamline their processes and improve stock control. These systems provide real-time updates on inventory levels, making it easier to monitor stock across multiple locations. An effective inventory system should offer the capability to track inventory accurately, manage inventory locations, and execute inventory transactions smoothly. Advanced management software solutions provide insights into field service operations and can help businesses maintain optimal product inventory levels. Implementing a comprehensive software solution offers several benefits, such as:- Real-time tracking: Providing instant updates on stock levels, enabling quick adjustments to avoid overstocking or understocking.
- Comprehensive field service management: Ensuring that field service providers have the necessary parts and items to complete tasks at different locations without delay.
- Order management: Automating order processing to optimize the order cycle and enhance customer satisfaction.
- Cycle counting: Frequently updating stock data to maintain accurate inventory levels and minimize errors.
Case Studies: Success Stories in Service Inventory Management
Real-Life Applications in Service Inventory Management
Exploring real-world applications offers valuable insights into effective service inventory management. By delving into case studies, businesses can learn from others' successes and challenges, improving their inventory strategies and processes. One compelling example is a logistics company that revolutionized its inventory control through innovative management software. By implementing a comprehensive system, the company effectively tracked stock levels across multiple locations in real time. This led not only to enhanced inventory control but also maximized customer satisfaction by ensuring timely deliveries. Another noteworthy case involves a retail chain that re-engineered its supply chain management. By employing advanced software, the company could precisely monitor its inventory locations and adjust stock levels accordingly. This proactive approach streamlined inventory transactions, reduced wastage, and boosted overall profitability. Moreover, a case from the field service industry highlights the significance of optimizing product inventory. A maintenance service provider integrated a robust system to manage inventory levels across scattered sites. This enabled rapid response times and reduced downtime, positively impacting customer satisfaction. Cycle counting has also proved beneficial in various sectors. For instance, a manufacturing business adopted this method to maintain accurate inventory levels. The process allowed for better planning, reduced discrepancies, and facilitated seamless order fulfillment. By analyzing these successful implementations, businesses can learn the importance of harnessing technology and innovative strategies for improved service inventories. These examples underline the necessity of a dynamic management approach, emphasizing adaptability and real-time data utilization.Future Trends in Service Inventory Management
Emerging Trends and Innovations in Service Inventory Management
As businesses continue to evolve, so does the approach to managing service inventories. There are several key trends that are making waves in the inventory management field, ensuring that even complex service inventories are handled with greater efficiency and effectiveness.
1. Integration of AI and Machine Learning: Advanced technologies like AI and machine learning are enabling businesses to forecast demand more accurately. By analyzing data patterns and trends, these technologies assist in maintaining optimal inventory levels and enhancing customer satisfaction. Predictive analytics, for instance, allows for more precise inventory transactions and efficient stock level management, significantly reducing the risk of overstocking or stockouts.
2. Real-Time Inventory Tracking: With improvements in technology, real-time tracking of inventory levels across multiple locations has become a reality. Businesses are now able to monitor their inventory transactions seamlessly, which aids in adjusting order processes timely and reducing inventory holding costs. This helps in streamlining the entire service inventory management process and supports dynamic supply chain adjustments.
3. Cloud-Based Solutions: The adoption of cloud-based inventory management systems is on the rise. These systems offer a centralized platform for tracking inventory locations, managing product inventories, and monitoring service levels. Businesses are leveraging cloud software to ensure that their inventory remains accessible and manageable across various locations, enhancing their field service operations.
4. Automation and Robotics: Automation technologies are increasingly being utilized to handle repetitive inventory control tasks. Robotics can be employed to perform cycle counting and manage stock levels, freeing up human resources for more strategic roles within business operations. The integration of automated systems contributes to accuracy and efficiency in inventory management.
5. Sustainability and Ethical Practices: Businesses are becoming more conscious of their environmental footprint, and this extends to inventory management practices. Taking a sustainable approach can involve efficient resource allocation, reducing waste, and optimizing supply chain processes. Innovative businesses are adopting circular economy principles to ensure their inventory practices are both environmentally friendly and cost-effective.
The future of service inventory management is shaped by these innovative trends and tools. Businesses that adapt to these changes are better positioned to thrive in a competitive market by enhancing their operational efficiency and providing exceptional customer service.